Lipstick tubes are the most complex and difficult of all cosmetic packaging materials. First of all, we must understand why lipstick tubes are difficult to make and why there are so many requirements. Lipstick tubes are composed of multiple components. They are functional packaging made of different materials. In terms of material body, it can be divided into volatile and non-volatile types . In addition, most of the filling is automatic filling by machines, including the loading of lipstick tubes, which is very complicated. The combination of different parts requires inconsistent tolerance control. Well, or the design is unreasonable, even if the lubricating oil is applied wrongly, it will cause downtime or malfunction, and these mistakes are fatal.
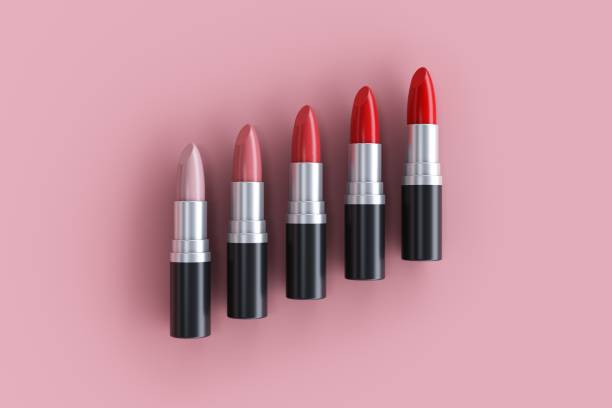
Lipstick tube base material
Lipstick tubes are divided into all-plastic lipstick tubes, aluminum-plastic combination tubes, etc. The commonly used plastic materials are PC, ABS, PMMA, ABS+SAN, SAN, PCTA, PP, etc., while the commonly used aluminum models are 1070, 5657, etc. There are also users who use zinc alloy, sheepskin and other materials as lipstick tube accessories in order to show that the product temperament is consistent with its brand tone.
The main functional parts of the lipstick tube
①Components: cover, bottom, center beam core;
②Medium beam core: medium beam, beads, forks and snails.
The finished lipstick tube usually includes a cap, a middle bundle core and an outer base. The middle bundle core includes a middle bundle part, a spiral part, a fork part and a bead part which are set in sequence from the outside to the inside. The bead part is set on the inside of the fork part, and the bead part is Used to place lipstick paste. Insert the assembled center beam core into the outer base of the lipstick tube, and then match it with the cover to obtain the finished lipstick tube. Therefore, the center beam core has become an important core component of the lipstick tube.
Lipstick Tube Manufacturing Process
①Component molding process: injection molding, etc.;
② Surface technology: spraying, electroplating, evaporation, laser engraving, inserts, etc.;
③ surface treatment process of aluminum parts: oxidation;
④Graphic printing: silk screen, hot stamping, pad printing, heat transfer printing, etc.;
⑤Inner material filling method: bottom, top.
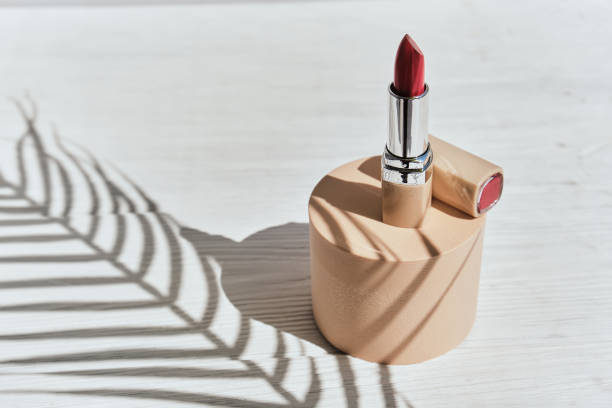
Quality control indicators of lipstick tubes
1. Basic quality indicators
The main control indicators include hand feel indicators, filling machine requirements, transportation vibration requirements, air tightness, material compatibility issues, size matching issues, aluminum-in-plastic tolerance and color issues, production capacity issues, and The filling volume should meet the declared value of the product.
2. The relationship with the material body
The lipstick material body has softness and hardness. If it is too soft, the cup is not deep enough. The material body cannot be held by HOLD. The lipstick flesh will fall out as soon as the customer applies lipstick. The material body is too hard and cannot be applied. The material body is volatile (lipstick does not discolor). If the air tightness is not good (the lid and bottom do not match well), it is very easy to cause the material body to dry out, and the entire product will fail.
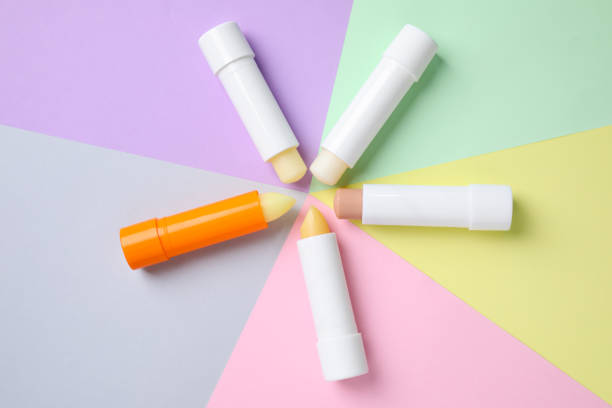
Development and design of lipstick tube
Only on the basis of understanding the reasons for various requirements can we design various test methods and standardize various indicators. Novices must choose mature snail designs and complete the universal snail design as soon as possible.
Post time: Sep-06-2023