Polyethylene (PE)
1. Performance of PE
PE is the most produced plastic among plastics, with a density of about 0.94g/cm3. It is characterized by being translucent, soft, non-toxic, cheap, and easy to process. PE is a typical crystalline polymer and has post-shrinkage phenomenon. There are many types of it, the commonly used ones are LDPE which is softer (commonly known as soft rubber or flower material), HDPE which is commonly known as hard soft rubber, which is harder than LDPE, has poor light transmittance and high crystallinity; LLDPE has very excellent performance, similar to engineering plastics. PE has good chemical resistance, is not easy to corrode, and is difficult to print. The surface needs to be oxidized before printing.
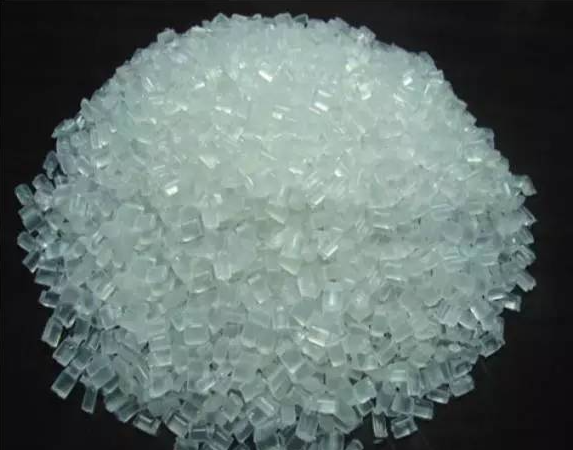
2. Application of PER
HDPE: packaging plastic bags, daily necessities, buckets, wires, toys, building materials, containers
LDPE: packaging plastic bags, plastic flowers, toys, high-frequency wires, stationery, etc.
3. PE process characteristics
The most notable feature of PE parts is that they have a large molding shrinkage rate and are prone to shrinkage and deformation. PE materials have low water absorption and do not need to be dried. PE has a wide processing temperature range and is not easy to decompose (the decomposition temperature is about 300°C). The processing temperature is 180 to 220°C. If the injection pressure is high, the product density will be high and the shrinkage rate will be small. PE has medium fluidity, so the holding time needs to be longer and the mold temperature should be kept constant (40-70°C).
The degree of crystallization of PE is related to the molding process conditions. It has a higher solidification temperature. The lower the mold temperature, the lower the crystallinity. . During the crystallization process, due to the anisotropy of shrinkage, internal stress concentration is caused, and PE parts are easy to deform and crack. Putting the product in a water bath in 80℃ hot water can relax the internal stress to a certain extent. During the molding process, the material temperature should be higher than the mold temperature. The injection pressure should be as low as possible while ensuring the quality of the part. The cooling of the mold is particularly required to be rapid and even, and the product should be relatively hot when demolded.
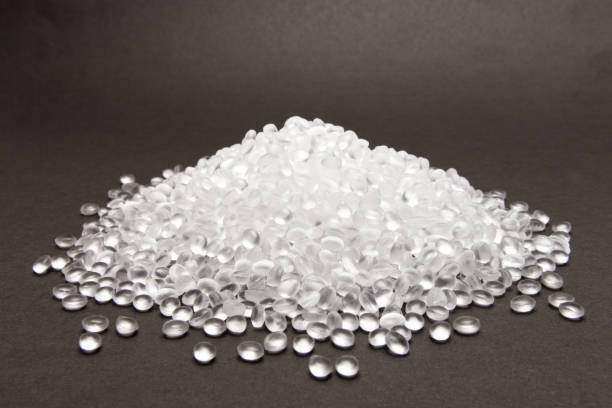
Polypropylene (PP)
1. Performance of PP
PP is a crystalline polymer with a density of only 0.91g/cm3 (less than water). PP is the lightest among commonly used plastics. Among general plastics, PP has the best heat resistance, with a heat deformation temperature of 80 to 100°C and can be boiled in boiling water. PP has good stress cracking resistance and a high bending fatigue life, and is commonly known as "100% plastic". ".
The comprehensive performance of PP is better than that of PE materials. PP products are lightweight, tough and chemically resistant. Disadvantages of PP: low dimensional accuracy, insufficient rigidity, poor weather resistance, easy to produce "copper damage", it has post-shrinkage phenomenon, and products are prone to aging, becoming brittle and deformed.
2. Application of PP
Various household items, transparent pot lids, chemical delivery pipes, chemical containers, medical supplies, stationery, toys, filaments, water cups, turnover boxes, pipes, hinges, etc.
3. Process characteristics of PP:
PP has good fluidity at the melting temperature and good molding performance. PP has two characteristics:
First: the viscosity of PP melt decreases significantly with the increase of shear rate (less affected by temperature);
Second: The degree of molecular orientation is high and the shrinkage rate is large.
The processing temperature of PP is better around 200~250℃. It has good thermal stability (decomposition temperature is 310℃), but at high temperature (280~300℃), it may degrade if it stays in the barrel for a long time. Because the viscosity of PP decreases significantly with the increase of shear rate, increasing the injection pressure and injection speed will improve its fluidity; to improve shrinkage deformation and dents, the mold temperature should be controlled within the range of 35 to 65°C. The crystallization temperature is 120~125℃. PP melt can pass through a very narrow mold gap and form a sharp edge. During the melting process, PP needs to absorb a large amount of melting heat (larger specific heat), and the product will be relatively hot after coming out of the mold. PP materials do not need to be dried during processing, and the shrinkage and crystallinity of PP are lower than those of PE.
Post time: Dec-28-2023