A Guide to Production Capacity in Topfeel
Production capacity is an important indicator for any manufacturer planning production.
Topfeel takes the lead in advocating the business philosophy of "cosmetic packaging solutions" to solve customers' problems in packaging type selection, design, production, and series matching. Using continuous technological innovation and mold production resources, we have truly realized the integration of the customer's brand image and brand concept.
Mold development and manufacturing
Molds are various molds and tools used in industrial production for injection molding, blow molding, extrusion, die-casting or forging forming, smelting, stamping and other methods to obtain the required products. In short, a mold is a tool used to make shaped objects. This tool is composed of various parts, and different molds are composed of different parts.
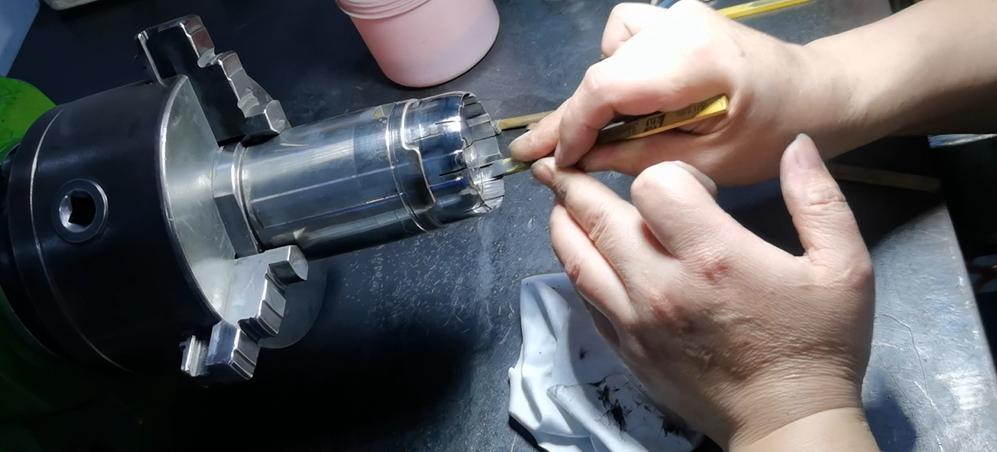
Mold composition:
1. Cavity: manual polishing is required, using S136 steel with a high hardness of 42-56.
2. Mold bases: low hardness, easy to scratch
3. Punch: the part that forms a bottle shape.
4. Die core:
① It is related to the life of the mold and the production period;
②Extremely high requirements on cavity precision
5. Slider structure: Left and right demoulding, the product will have a parting line, which is mostly used for special-shaped bottles and jars that are difficult to demould.
Other equipment
Grinder
• The most precise equipment in the whole mold production process.
• Small grinder: can process round and square molds, use industrial alcohol to cool down, manual operation.
• Large grinder: only handle square molds, mainly handle the right angle of the mold base; emulsified oil cooling; machine operation.
Drill press
Drilling machine: processing the screw hole of the mold.
Milling machine: rough machining screw holes, and can also cut molds.
Automatic tapping machine: thread processing of molds
①The teeth of the screw teeth are neat
②The verticality of the thread is good
Conventional machine tools
- Processing round molds, the tool used is tungsten steel, tungsten steel high hardness, small wear and tear in use, strong cutting ability, but brittle texture, fragile.
- Mostly used for punches, cavities and other round parts processing.
CNC machine tools
- Roughing molds. Use tungsten carbide cutter, use emulsified oil for cooling.
- When cutting, align all the tools (counterblade)
Production and assembly process
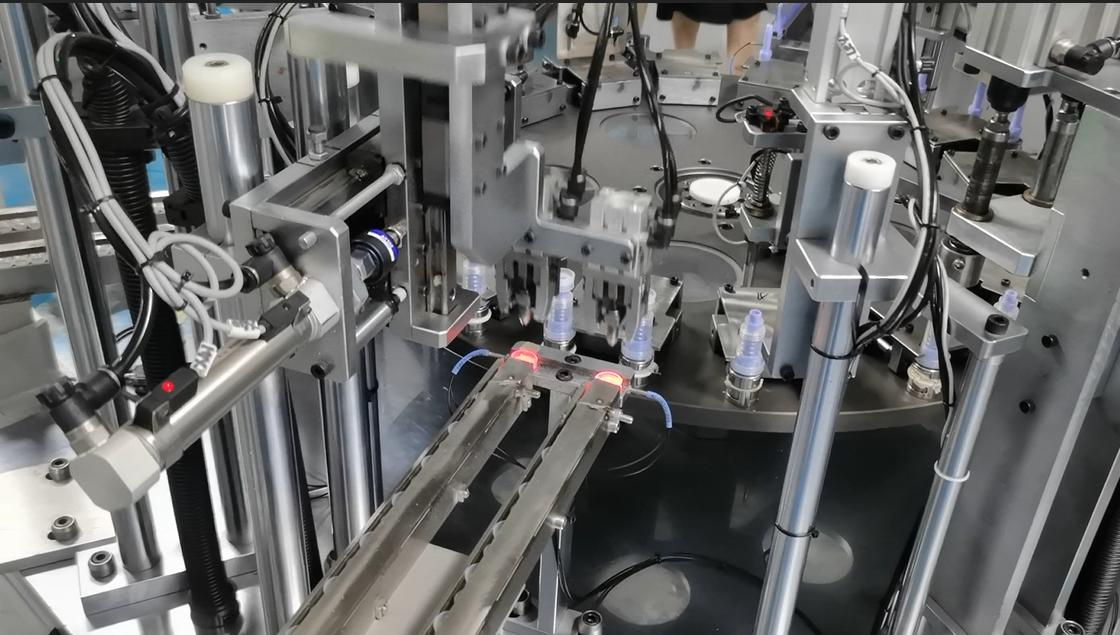
The assembly process of the pump core
Piston rod, spring, small piston, piston seat, cover, valve plate, pump body.
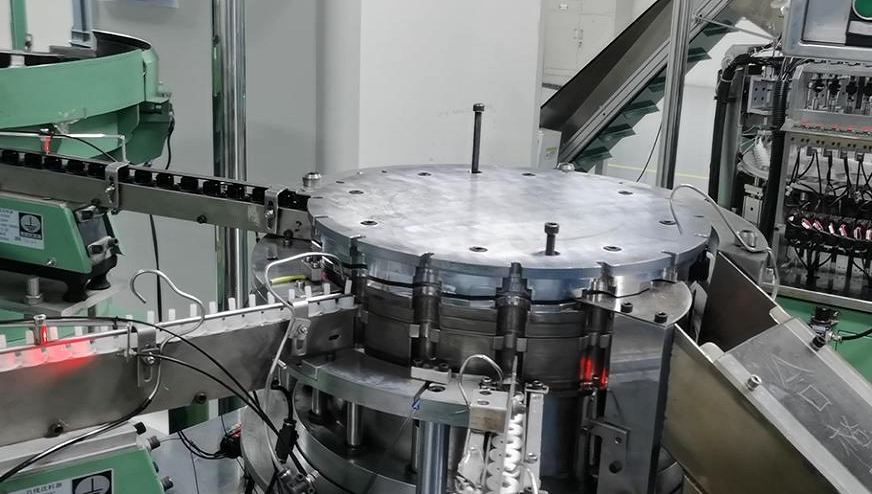
The assembly process of the pump head
Check-place-dispensing-press pump core-press pump head.
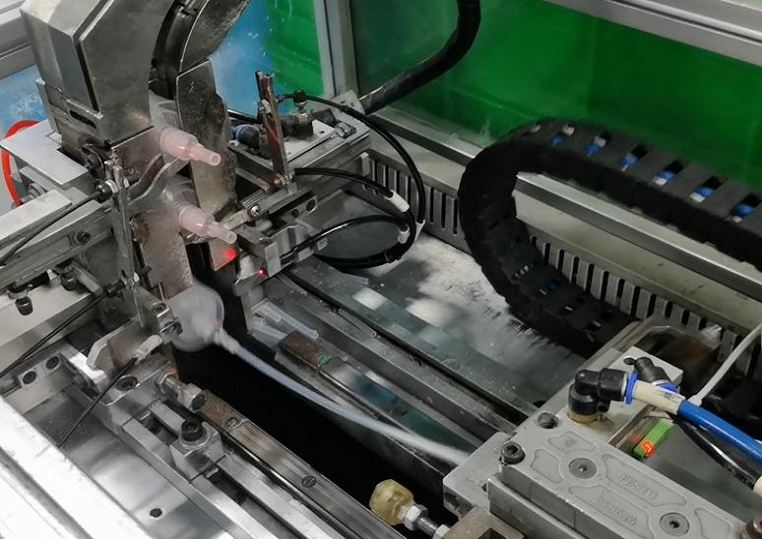
The assembly process of the straw
Feeding material-mold (pipe forming)-setting water pressure control pipe diameter-water path-outlet straw.
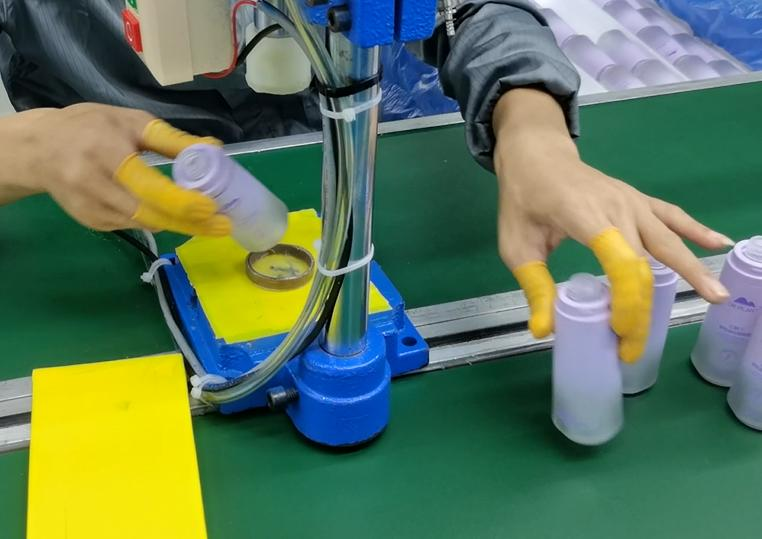
The assembly process of the airless bottle
Add silicone oil to the bottle body-piston-shoulder sleeve-outer bottle-test air tightness.
Craft production process
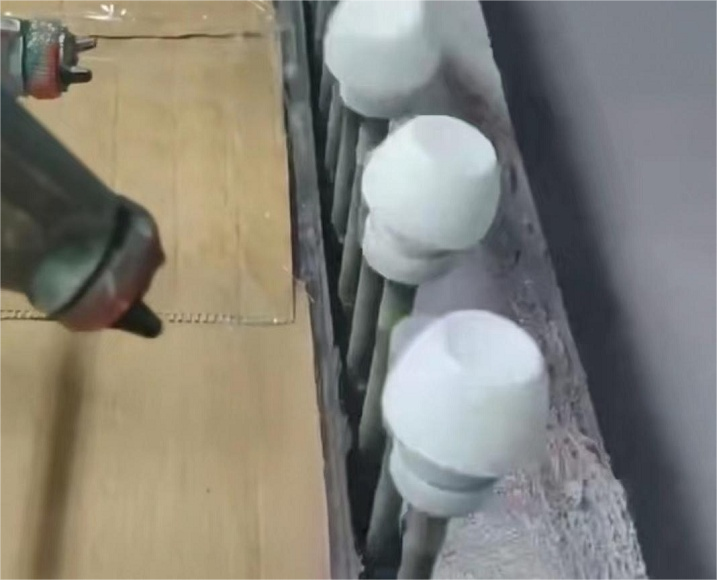
Spraying
Apply a layer of paint evenly on the surface of the product to achieve the desired effect.
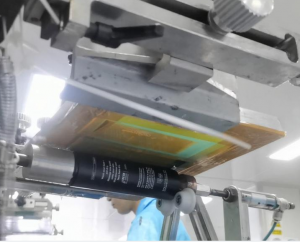
Screen printing
Printing on the screen to form an image.
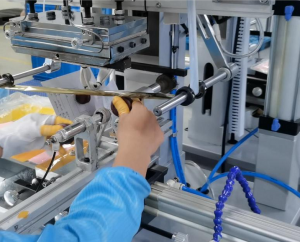
Hot stamping
Print text and patterns on hot stamping paper under high temperature and high pressure.
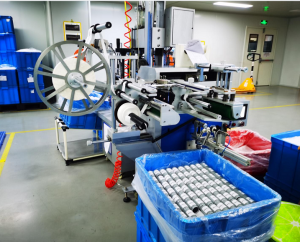
Labeling
Use the machine to label the bottles.
Product quality test
Inspection process
Raw material
Production
Packaging
Finished products
Inspection standards
➽Torque test: Torque = threadprofile diameter/2 (qualified within the range of plus or minus 1)
➽Viscosity test: CP (unit), the thicker the test tool is, the smaller it is, and the thinner the test tool is, the bigger it is.
➽Two-color lamp test: international color card resolution test, the industry's common light source D65
➽Optical image test: For example, if the test result of the dome exceeds 0.05 mm, it is a failure, that is, deformation or uneven wall thickness.
➽Break test: The standard is within 0.3mm.
➽Roller test: 1 product + 4 screw tests, no sheet falling off.
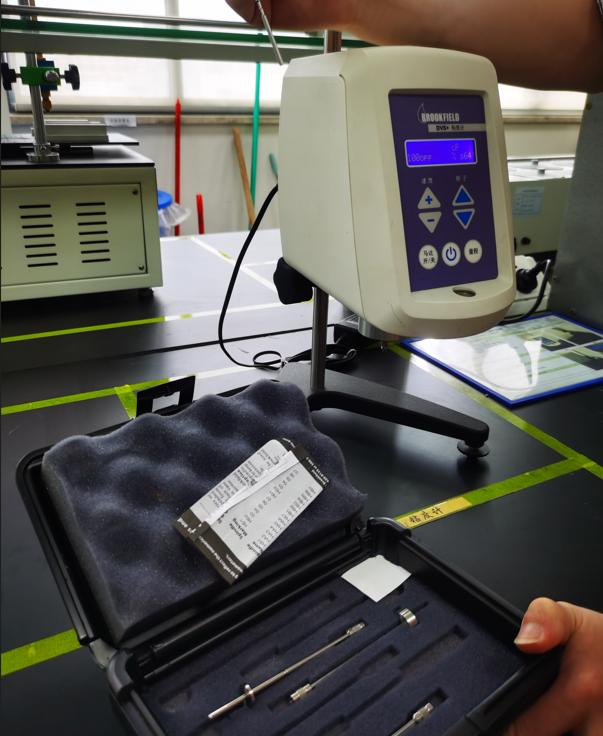
➽High and low temperature test: The high temperature test is 50 degrees, the low temperature test is -15 degrees, the humidity test is 30-80 degrees, and the test time is 48 hours.
➽Abrasion resistance test:The test standard is 30 times per minute, 40 back and forth frictions, and a load of 500g.
➽Hardness test: Only sheet gaskets can be tested, the unit is HC, other hardness molds have standards and a monitoring system.
➽Ultraviolet weather resistance test: To measure aging, mainly to see discoloration and process shedding. 24 hours of testing is equivalent to 2 years under normal environment.
